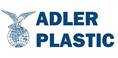



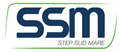
Hy_COMPO_2020 – Hybridized Composite and Powertrain system for Europe 2020
Sviluppo di tecnologie innovative per l’ibridazione dei compositi strutturali e dei sistemi di motopropulsione per la mobilità sostenibile
Contesto | Il progetto di ricerca rientra nel Programma Operativo Nazionale 2007-2013, D.D. 713/Ric. Nuovi Distretti e Laboratori - Titolo 3 e si colloca nel Settore/Ambito: Trasporti e Logistica. |
Soggetti Attuatori | ANFIA AUTOMOTIVE, con i soci: Adler Plastic, Step Sud Mare, MecapromCERICT e TEST, tramite le seguenti Università:- Università degli Studi di Salerno- CNR IPCB |
Sintesi | Obiettivo del progetto è lo sviluppo di soluzioni innovative complementari tese adincrementare l’efficienza dei veicoli grazie all’impiego di logiche di ibridazione ad oggetto i materiali compositi per i componenti veicoli e i sistemi di motopropulsionecon le relative architetture, attraverso la ricerca di nuovi modelli in grado di integrare sinergicamente gli sviluppi massa veicolo-sistema motore.Individuando un possibile percorso di sviluppo che porti alla progressiva decarbonizzazione del Settore dei Trasporti, il progetto affronta le sfide che l’Industria dei Trasporti su Gomma dovrà affrontare per guadagnare competitività nei prossimi anni:• riduzione del 60% delle emissioni dei trasporti entro la metà del secolo• esclusione delle Auto con alimentazione convenzionale dai centri urbani• definizioni di meccanismi legislativi per cui "chi inquina paga" & "chi usa paga" tassando in modo differenziato le esternalità negative.Con il contributo di tutti i partner sono stati definiti e modellati gli scenari di riferimento per il trasporto su gomma, considerando gli aspetti fisici, tecnologici, economici, di mercato e le caratteristiche del territorio. Sono stati ipotizzati trend economici ed evoluzioni dei mix tecnologici considerati rilevanti e curato il raccordo con le linee-guida Europee e con i risultati dei Progetti Nazionali attualmente in corso. Definiti gli scenari della mobilità e del trasporto a medio-lungo termine, sono stateidentificate le soluzioni tecniche sostenibili ed efficaci nelle aree ritenute più promettenti, che possono essere schematizzate in:• Alleggerimento basato sull’ibridazione dei materiali compositi e incremento dell’efficienza passiva• Ibridazione del sistema di motopropulsore del veicolo quale soluzione ottimale per una mobilità sostenibile nel breve medio-periodo, propedeuitica ad una mobilità completamente elettrica |
Durata | 1 Gennaio 2014 – 31 Marzo 2017 (39 mesi) |
Hy_COMPO_2020 - Attività e risultati |
I risultati del progetto sono stati innanzitutto la progettazione, completa di validazione strutturale, del dimostratore tecnologico individuato (struttura sedile posteriore), attraverso una attività di re-engineeringche, a partire dalla soluzione di riferimento realizzata in tecnologia tradizionale (tubolari in acciaio saldati), fermo restando i vincoli di lay-out e prestazionali del componente (in particolare dell’urto per intrusione bagaglio posteriore), e tenendo conto dei vincoli di fattibilità della tecnologia innovativa individuata e sviluppata, ha portato ad una riduzione di peso complessiva del componente pari al 15%. La validazione strutturale della soluzione reingegnerizzata è stata completata grazie ad attività di testingsperimentali sui materiali individuati a progetto, sia statica che dinamica.La tecnologia innovativa individuata è quella della termoformatura di materiali compositi a matrice termoplastica (CFRTP), con successiva retro-iniezione (“HYBRID TECHNOLOGY”), che consiste nelle due seguenti macro fasi:- termoformatura di una lastra preconsolidata costituita da tessuto di rinforzo a fibre lunghe (carbonio o vetro) impregnate in una matrice polimerica termoplastica (PA6 nylon nel caso specifico), tramite preriscaldo della lastra in forno ad infra rossi fino al melting point del polimero e successivo stampaggio della stessa sotto pressa con stampi metallici preriscaldati.- retro-iniezione dello stesso polimero di cui è formata la lastra preconsolidata (PA6 nel caso specifico), eventualmente caricato con fibra corta vetro/carbonio riciclato, per la formazione di nerve di irrigidimento o integrazione di inserti metallici/complicazioni geometriche.Il suddetto processo è stato sviluppato attraverso la realizzazione di “sub-componenti” significativi, sui quali, attraverso la realizzazione di stampi prototipali e la modifica di impianti esistenti, è stata eseguita la messa a punto di tutti i parametri di processo e sono state individuate le linee guida per la progettazione e la realizzazione delle attrezzature necessarie per la realizzazione del dimostratore finale.A valle di questa fase preliminare di sviluppo e messa a punto è stato possibile progettare gli stampi sia di termoformatura che di retro iniezione del dimostratore finale, per procedere poi alla fase realizzativa dei dimostratori e di testing sperimentali degli stessi volti a validare il prodotto ed il processo innovativo sviluppati.Parallelamente ed in modo sinergico, si è proceduto alla definizione dello scenario tecnologico e normativo dei sistemi di motopropulsione ibrida elettrica e ad identificare lo stato dell’arte delle tecnologie e dei componenti più rilevanti, quali il gruppo di accumulo, i motori elettrici e i controllori di potenza, al fine di realizzare modelli e simulazioni dei sottosistemi e dell’intero veicolo, rapportandoli all’applicazione dei regolamenti omologativi e degli standard di valutazione delle prestazioni. L’oggettivazione dei dati forniti dall’attività di calcolo ha poi permesso di realizzare la comparazione fra le soluzioni tecnologiche presenti sui veicoli ibridi di attuale produzione e quelle contenute nella proposta C-Hybrid, consentendo la cattura dei parametri funzionali e comportamentali significativi per il dimensionamento dei sottosistemi e componenti ausiliari, finalizzati alla definizione di soluzioni migliorative, rispetto a quelle ad oggi adottate. Sono state definite soluzioni mirate a recuperare i costi, i pesi e gli svantaggi derivanti dalla maggior complessità dell’architettura C-Hybrid, rispetto ad architetture di powertrain convenzionali e puro elettrico, agendo in particolare sull’ottimizzazione dei flussi energetici, per ridurre capacità, peso e costo della batteria, diminuire e semplificare le caratteristiche del motore endotermico conseguenti alla riduzione delle richieste di dinamica, produrre un effetto positivo in termini di “ansia da autonomia” e minimizzare i disagi conseguenti all’attivazione del motore endotermico. Si è intervenuti sul dimensionamento dei materiali e delle forme dei componenti del motore endotermico, al fine di massimizzare i benefici determinati dall’architettura V-Twin, producendo soluzioni innovative per il basamento, la biella e il suo piede, l’albero motore e il collettore di aspirazione.Analogamente, il sistema di trasmissione a doppia frizione e cinghia di trasmissione, così come la costruzione meccanica delle macchine elettriche, è stata ottimizzata nei pesi e nelle rigidezze torsionali, tramite l’utilizzo di forme e materiali alleggeriti. A valle, è stato progettato e sviluppato un sistema di controllo ottimo dei flussi energetici, tale da determinare la gestione della transizione dei percorsi di potenza secondo un funzionale di costo, determinato con tecniche di Dynamic Programming. Infine si è proceduto a realizzare i componenti ed i sottosistemi di trazione, assemblando il gruppo di motopropulsione, accumulo e controllo nel veicolo dimostratore, validato attraverso test sperimentali e di messa a punto a banco e su strada. |

Nell'area download è possibile scaricare la scheda completa del Progetto in pfd.